How to Build a Timber Frame Extension
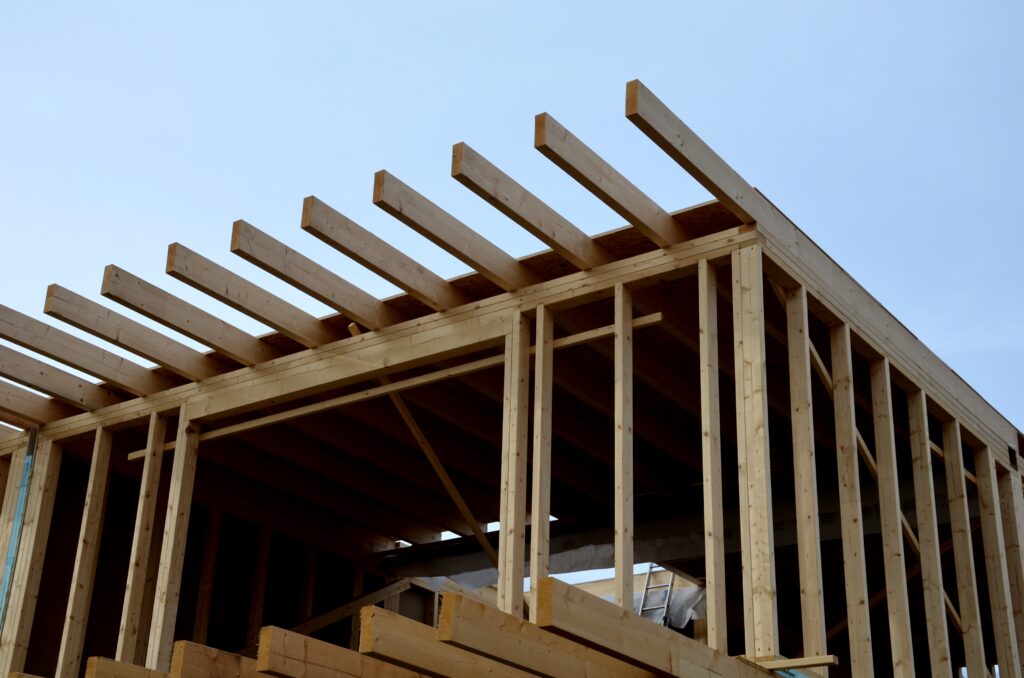
When it comes to planning a home extension, the choice of building method is a critical decision. The traditional masonry approach, using bricks and mortar, has been a staple in the UK. While block-build retains its devotees, there’s a discernible shift in favour of timber frame house extensions.
Timber frame is versatile, applicable to a range of structures from schools to flats and home extensions. Below, we present a comprehensive guide to help you determine if timber frame is the right choice for your project. We also outline the basics of how to build a timber frame extension.
As ever, before embarking on any construction project, we advise that you consult a professional.
Understanding Timber Frame Construction
Timber frame construction entails using a wooden frame to distribute both vertical and horizontal loads to the foundation.
The load-bearing timber frame, usually concealed within the void between external bricks and internal plasterboard, can look identical to brick and block extensions, negating concerns about appearance.
A variation of this is the post and beam timber frame, where certain structural elements remain exposed, such as roof trusses and rafters. Additionally, a combination of post and beam and timber frame panels can be employed.
Crafting the Timber Frame Structure
Most timber frame extensions are meticulously constructed on-site, with the stud framework erected incrementally according to unique designs.
This framework, serving as the load-bearing skeleton of the external wall, comprises vertical studs and horizontal rails. Strength-graded timber, treated against rot and infestation, is essential for these structural elements’ durability. Subsequently, wall panels are affixed to the frame.
On the exterior, the timber frame construction offers versatility in cladding options, allowing for the use of various materials such as timber panels, bricks, render, or stone. These choices empower you to harmonise with the existing aesthetic of your residence or make a contemporary statement that sets it apart.
Door and window openings are usually reinforced with extra studs to support load-bearing lintels. The interior of the frame is typically lined with plasterboard, contributing to the wall’s fire resistance.
Insulation is placed within the cavities between the studs and rail framing, while external cladding is often achieved using brick connected to timber wall panels through steel wall ties.
Remember, although planning permission might not always be required for an extension, obtaining approval from building regulations is essential.
Prior to commencing any work, it’s crucial to verify with your local governing body, particularly if your property is listed, situated within a conservation area, or falls under the designation of an Area of Outstanding Natural Beauty.
Designing Your Timber Frame Extension
The design of your timber frame extension can be orchestrated by any architect familiar with timber frame construction.
Additionally, kit suppliers offer a spectrum of services, ranging from providing the frame to managing the on-site build.
Suppliers can manufacture internal partitions, roof trusses, floor and ceiling joists off-site in a factory, streamlining the assembly process.
Off-site construction, also known as modular construction, has witnessed a resurgence in recent times, building upon the legacy of prefab homes from the post-war era.
The speed advantage of timber frame construction lies in its efficiency, particularly when panels are prefabricated off-site.
Accounting for Differential Movement in Anticipated Timber Frame Structures
It’s important to recognise that timber frame structures will experience differing degrees of movement in comparison to the masonry cladding on their exterior surfaces. This aspect necessitates careful consideration from the structural engineer.
To accommodate this horizontal and vertical movement, the inclusion of movement joints becomes essential. Place these joints strategically beneath all openings, as well as at eaves and verges.
Furthermore, any element or component affixed to the timber superstructure that extends beyond the brick or blockworkâsuch as cladding fastened to the timber frame, window sills, roof eaves, and vergesâor projects through the masonryâsuch as balcony supports, flues, extractor fan vents, or overflow pipesâmust maintain a distinct gap both beneath and above the masonry cladding. This clearance is vital to facilitate the occurrence of differential movement, preventing harm to these components or the cladding itself.
The measurements of these gaps should accommodate the expected variance in movement while still allowing for necessary drainage and ventilation considerations.
Advantages of Timber Frame Construction
Accelerated Construction
Timber frame construction builds faster than traditional brick and mortar, especially when factories fabricate the panels.
Workers can erect panelled walls faster than individual bricks or blocks, potentially making the structure weatherproof in just a few days.
This expedites subsequent interior trades, such as electrics and plastering.
Moreover, the term “wet trade,” referring to trades involving water-mixed materials like brickwork and mortar, underscores timber frame’s advantage. Unlike brick and blockwork, timber frame construction eliminates the drying time required for mortar, allowing construction to proceed even in cold and wet weather conditions.
Strength and Flexibility
Despite common misconceptions, timber frame constructions are robust and durable, enduring harsh weather conditions. They must adhere to Building Regulations, including fire protection, akin to brick and block walls.
Timber’s lightweight nature not only facilitates transportation but can also reduce foundation costs depending on ground conditions.
Design flexibility is another hallmark of timber frame construction. The method accommodates various architectural visions, facilitating the creation of spacious open-plan extensions with vaulted ceilings.
Incorporating exposed structural steelwork can lend a contemporary touch, providing opportunities for unique design elements.
Sustainability and Energy Efficiency
Timber’s renewable and eco-friendly characteristics position it as an environmentally conscious building material. Sustainable sourcing is key, ideally adhering to standards like the Forest Stewardship Council logo, signifying responsible forestry practices.
Timber’s conversion into a usable building material consumes less energy and generates less pollution compared to materials like steel and concrete.
Both timber frame and cavity wall constructions can be energy-efficient with high levels of insulation. Timber frame excels in achieving low U-values without significantly increasing wall width. While timber frame buildings are less soundproof than masonry, insulation of external walls, floors, and ceilings contributes to overall soundproofing.
Budget and Cost Effectiveness
Is a timber frame extension cheaper than other traditional methods? In most scenarios, a timber frame extension indeed comes at a lower cost than extensions built using traditional methods.
Timber frame extensions can be cost-effective, primarily due to reduced skilled labour requirements. For instance, when considering an added roof storey, the timber frame option typically proves more economically viable than blockwork.
How much will a timber frame extension cost in total? Costs average around ÂŖ1,300 per m2 of floor area, with variables like frame type, glazing, cladding, and location affecting the final price.
While certain timber frame variations might increase costs, such as a post and beam frame showcasing substantial timber sections, the overall budget advantage remains.
Conclusion
Building a timber frame extension offers numerous benefits, from expedited construction to design flexibility, sustainability, and energy efficiency.
The modern era has witnessed timber frame construction rising to prominence, proving its mettle against traditional methods.
With the potential to be cost-effective and environmentally friendly, timber frame extensions stand as a testament to the harmony between innovation and sustainability in the world of construction.